Okay, now is a good time to show you how to make up your pillow blocks (axle carriers)
I use ¼ wide by 1/16 thick brass stock to make mine up..
Start out by using a center punch to mark where you want to drill your hole. The punch mark will help keep the drill bit
from wandering when you start drilling. Drill the hole using a 3/32 drill bit
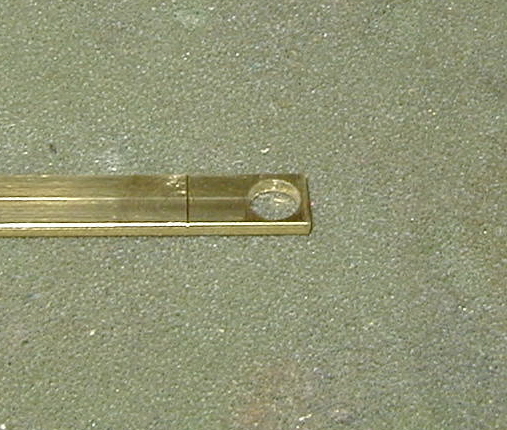
I have made up a little jig to help me make the pillow blocks and lay out the cut off lines to make them the right height
I took a piece of counter top I had laying around and drilled a set of 3/32 holes and put in some 3/32 piano wire
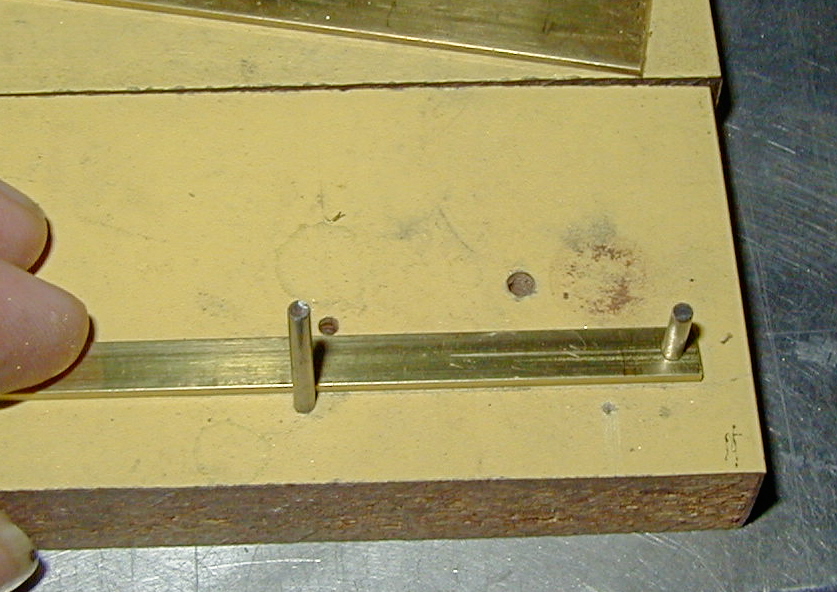
Now you need to find out how tall to make the pillow blocks.. For this you need to measure from then top of the axle to
the top of the JIG PLATE.. Not the top of the chassis pan.... With some dial calipers This will give you the height
that you need to make the pillow block.... this is done the same for the front and rear pillow blocks....
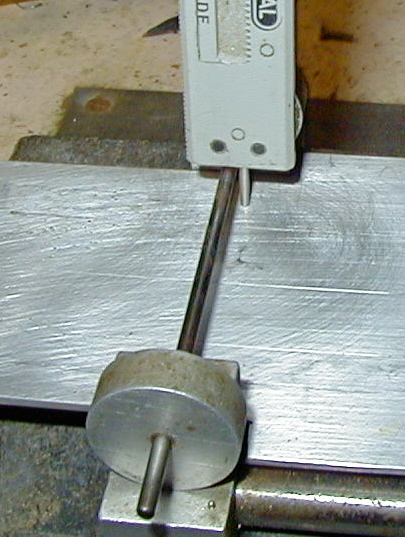
This will give you the height for the pillow block now using the handy little jig, mark out the pillow block cut off line..
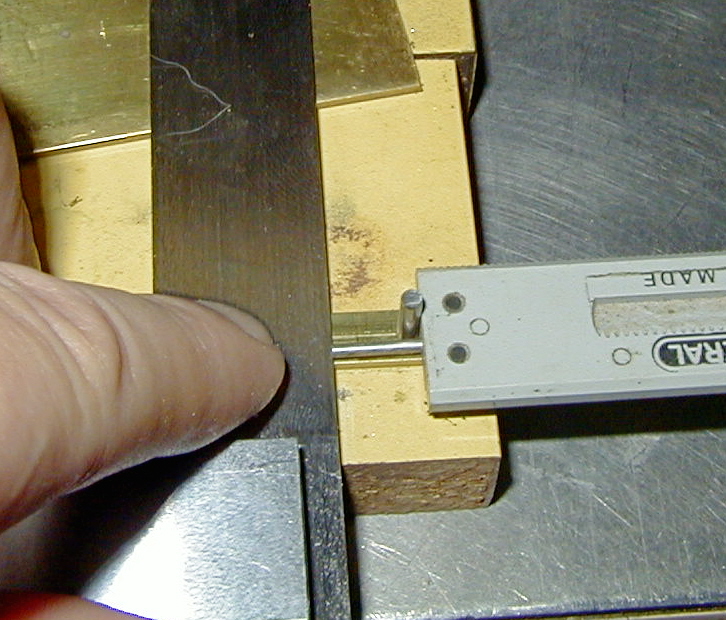
After you have scribed the cut off line, drill the 3/32 hole out to 1/8.. This will allow you to put a 1/8OD piece of brass
tubing into the hole to make up your front axle carrier. In this case I am using 3/32 axles Then cut off at the line.. After
all of the pillow blcoks are done test fit them to make sure you have the right height.. Your jig wheels should be touching
the chassis jig.. If they are not you need to file off some of the bottom of the pillow block until they are touching...
For the rear pillow blocks you would drill out the 3/32 hole to what ever size oilets (axle bushings) you are using to
take your rear axle. On my chassis I like to use a 3/32 by 3/16 oilet for my rear axles.
-----------------------------------------------------------------------------------------------------------------------
Okay, now you are ready to do some soldering.... put your pillow blocks on the axles with the spacers you need to keep
them in place and then fit the pillow blocks to the cut outs you made in the chassis... Once again check the fit of the blocks
and then solder the pillow blocks to the chassis pan.....
For me this means using a torch.. I do all my soldring with a propane torch.. When working with thick brass (.064) like
I do I have found that a torch is much quicker and easier to solder with and I get a much better solder flow with the torch...
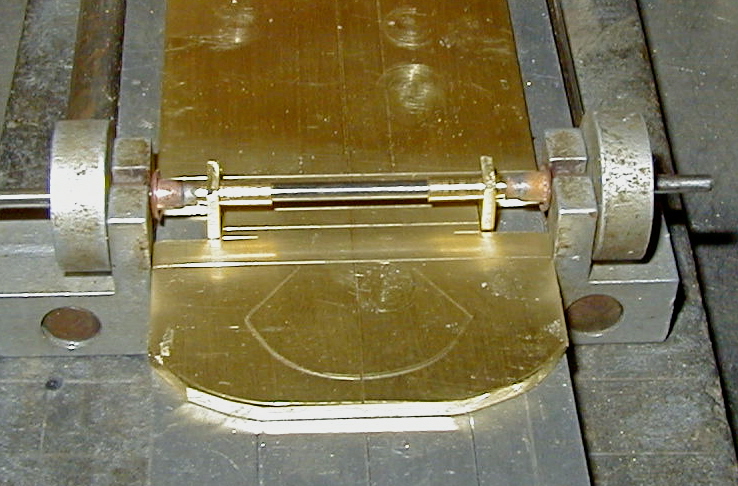
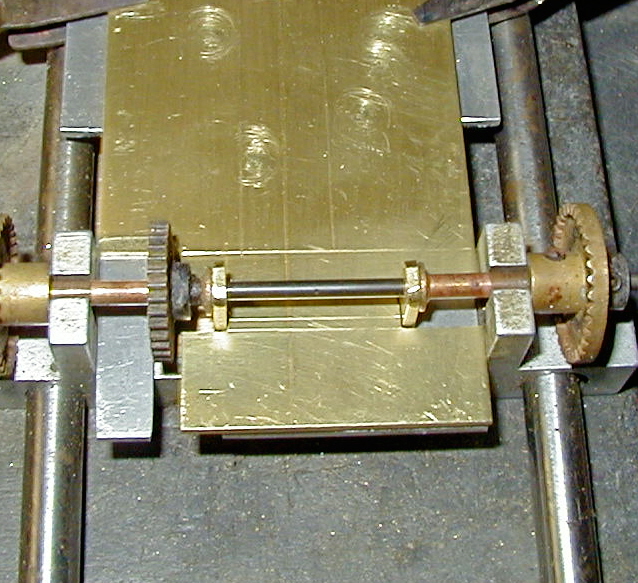
|
Do the same for the rear pillow blocks |
----------------------------------------------------------------------------------------------------------------------
Well, those are the basics to get started with your building. Besides the soldering which takes some practice, The hardest
part is handling the Dremal and learning to cut with that. Again practice is the key to working with any tool.....
To finish up the chassis you can check the article on the Torsion Bar chassis..
Well, what are you waiting for guy!!!! Get building :-)
|